How to Maximize Your Warehouse Space with Junk Removal
A warehouse that’s overrun with unused items becomes more than just an eyesore—it becomes a barrier to operational efficiency. As businesses grow, warehouse space becomes a critical asset. When clutter takes over, it limits productivity, blocks essential workflows, and makes every task more complicated than it needs to be. This is where the value of professional junk removal comes in. It’s not about simply throwing things away—it’s about reclaiming space, reshaping workflow, and revitalizing business operations from the inside out.
When piles of old equipment, broken furniture, or outdated inventory sit untouched, it creates an illusion of “busy-ness.” But this busyness is deceptive. It’s not productivity—it’s just chaos with a mask on. Removing the junk, the truly unnecessary, breathes clarity into a warehouse’s daily rhythm. The transformation isn’t just physical. It impacts decision-making, resource allocation, and team morale.
Why Decluttering is a Game-Changer in Warehousing
Maximizing space doesn’t necessarily mean adding square footage. Sometimes, it’s as simple as making better use of what you already have. Clutter consumes volume, yes, but it also consumes focus. When boxes teeter on top of forgotten pallets and unused shelving becomes a storage graveyard, you lose visibility into what’s essential. A warehouse free from junk operates like a well-oiled machine.
Removing junk allows room for more organized inventory management. It opens up aisles, frees up shelving, and cuts down the time staff spends maneuvering around obstacles. These small changes compound quickly into major operational advantages. Fewer accidents. Faster fulfillment. Higher employee efficiency. Decluttering with intention becomes an investment, not a cost, especially when done systematically and with professionals who understand the stakes.
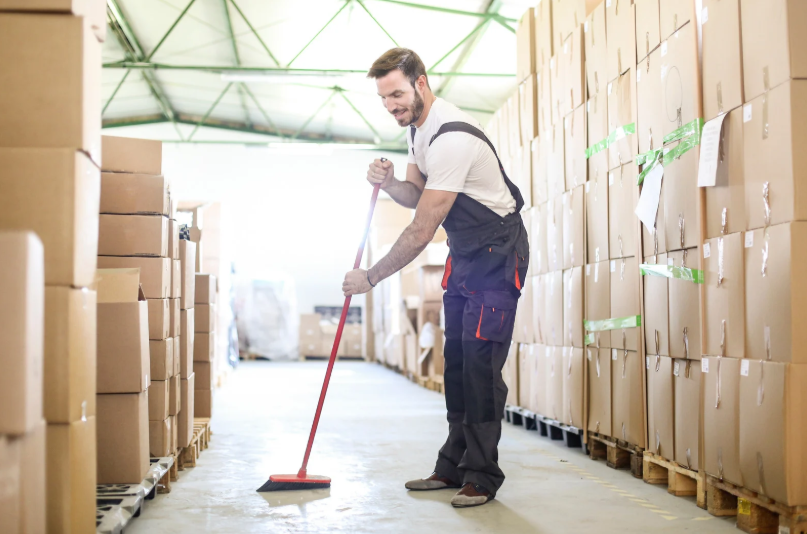
Reclaiming Floor Space for Profitable Use
In a world where warehouse real estate comes with a hefty price tag, every square foot should be pulling its weight. That means evaluating what’s truly contributing to your bottom line—and what’s just taking up space. Old packing materials, broken pallets, unused machines—these things quietly claim valuable real estate while offering no return.
Junk removal shifts that balance. It liberates areas that can be repurposed for value-added tasks: assembly stations, additional racking, or even a break area that doesn’t feel like an afterthought. More space can also lead to better layout planning. When you’re not boxed in by clutter, you can rearrange for optimal traffic flow, ergonomic access, and quicker turnarounds. What looks like a clean-up on the surface is often the first move in a broader warehouse strategy.
Inventory Accuracy Improves When Junk Disappears
The irony of junk is that it often hides in plain sight. Misplaced or outdated stock might sit quietly for months—or even years—masquerading as useful inventory. This creates ripple effects across your tracking systems, your counts, and ultimately, your customer service. Every misplaced pallet is a liability in waiting.
Once a professional junk removal service clears the clutter, your warehouse staff can engage more accurately with inventory. There’s less confusion, fewer phantom stock entries, and better use of barcode or RFID systems. It also reduces shrinkage—when everything is in its right place, it’s harder for items to be “lost.” What’s left after a junk purge is not just more space, but more certainty.
Safer Work Environments Start With Clean Floors
In any warehouse, safety isn’t just a checklist—it’s a living, breathing necessity. When clutter starts building up, the dangers sneak in quietly. Tripping hazards become part of the daily walk. Emergency exits hide behind boxes. That one broken pallet? It's still leaning in the corner. The reality is this: the more stuff in the way, the more risk your team faces. Whether it’s blocked aisles, dusty equipment, or unstable stacks of old packaging, safety takes a direct hit when junk piles up.
But a proper junk removal sweep doesn’t just make things look nice—it changes how the space functions. Forklift drivers glide instead of zigzagging. Fire marshals breathe easier. Pests lose their hiding spots. And workers feel more secure moving through the warehouse with confidence, not caution. A clear floor is a clear mind. Clean, visible pathways mean fewer accidents and quicker responses when something goes wrong. Even small adjustments can lead to big improvements, especially when every square foot matters.
Better Space Equals Better Productivity
Your environment is either lifting your team up—or dragging them down. In a warehouse packed with clutter, it’s hard to move quickly or think clearly. Workers navigate around old inventory, dodge forgotten carts, and waste time locating essential tools buried beneath debris. Over time, this frustration builds. Energy dips. Mistakes rise. It’s a cycle of fatigue, fueled by disorder. But when you remove the nonessential, everything starts to shift. The space begins to work with your team instead of against them.
Junk removal is more than tossing out trash. It’s an invitation to build momentum. Open space boosts morale. Workers aren’t just faster—they’re happier, more engaged, and less prone to error. Visual simplicity translates to mental clarity. With fewer distractions, decisions become sharper. Coordination improves. And daily tasks stop feeling like an uphill climb. The result? A team that operates with flow, not friction. Increased productivity isn’t always about new tech or bigger teams. Sometimes, it’s about making room—literally—for your people to move, think, and do their best work without clutter in the way.
A Fresh Start Makes Way for Lean Operations
Lean warehousing is more than just a buzzword—it’s a philosophy of continuous improvement and intentional use of resources. Clutter and junk go against everything lean stands for. Holding on to obsolete equipment or unused supplies "just in case" may feel safe, but it eats up budget and space.
Junk removal supports lean practices by helping warehouse teams regularly audit what they need versus what they’ve just gotten used to having around. It shifts the culture from one of accumulation to one of evaluation. The more agile your operation becomes, the better you can respond to market changes, volume spikes, or seasonal fluctuations. A lean, clutter-free warehouse is a warehouse that’s ready for anything.
Expanding Without Relocating
When growth comes knocking, most companies think expansion. But before you scout new buildings or negotiate higher rent, ask yourself: are we using every inch of what we already have? Often, the answer is no—because unused or junk items are taking up space meant for progress.
A full-service junk removal can delay or even eliminate the need for relocation. By opening up storage areas, converting underused rooms, or creating new access paths, companies can expand their capacity without expanding their footprint. It’s a more sustainable and cost-effective growth strategy. The warehouse you need might already exist—you just haven’t cleared the way to see it yet.
Sustainability and Responsible Disposal Practices
Modern businesses are increasingly judged by how they treat the environment. Dumping warehouse junk into landfills without a second thought isn’t just bad optics—it’s bad business. Partnering with a junk removal company that emphasizes recycling and donation ensures that your cleanout aligns with your sustainability goals.
Materials like metal, wood, electronics, and even some packaging can be redirected away from waste streams and into repurposing channels. With the right partner, you don’t have to choose between efficiency and ethics. You can clear space while doing your part for the planet, maintaining compliance with environmental guidelines, and even building goodwill with eco-conscious customers.
Streamlined Logistics Start with Open Space
Every box has a journey. From dock to shelf to truck, the smoother that journey is, the more successful your logistics process becomes. When your loading areas are clogged with unused materials or abandoned equipment, delays are inevitable. The bottlenecks start small—but they snowball fast.
Junk removal gives you room to design proper staging areas for inbound and outbound logistics. It frees up the space necessary for clear labeling, easier sorting, and efficient load planning. Drivers can dock and unload without navigating an obstacle course. Speed and accuracy increase. Errors decrease. With space finally optimized, your entire logistics chain gets tighter, faster, and more reliable.
Boosting Morale and Company Culture
A warehouse is more than just shelves and steel. It’s the place where your team spends most of their waking hours. When that environment is cluttered, dusty, and chaotic, it seeps into the culture. People start working just to get through the day—not to build something they’re proud of.
Cleaning out junk breathes pride back into the workspace. It signals to employees that their time and space are respected. It creates a feeling of movement—like the company is evolving, not stagnating. Culture begins with environment. And a clean, functional warehouse sets a tone of care, momentum, and forward-thinking leadership.
Conclusion
Optimizing your warehouse isn’t about doing more—it’s about doing better. Junk removal is one of the most overlooked yet powerful strategies for unlocking the full functionality of your warehouse. It’s not just about getting rid of old furniture or unused equipment—it’s about making room for smarter operations, faster logistics, and a more motivated team. When the clutter is gone, workflows open up. Inventory becomes easier to manage. Safety improves. Your space starts working for you instead of against you.
If your warehouse in Gwinnett Co feels more congested than productive, it might be time for a reset. Lasso & Load Junk Removal specializes in helping businesses like yours reclaim control over their environments. Whether it’s clearing out outdated stock or removing forgotten debris, their professional team brings clarity and purpose back to your space. Don’t wait until inefficiency costs you time and money—take the first step toward transformation. Reach out today at 404-227-2017 or email Lauren.renwickk@gmail.com. Your best warehouse layout might already exist. It’s just waiting to be uncovered, cleaned out, and put back to work.